Съемка подкрановых путей. Обоснование необходимости рихтовки рельсовых путей кранов мостового типа
Одним из «больных» вопросов на большинстве предприятий, эксплуатирующих краны мостового типа, является ремонт или замена ходовых колес и замена рельсов вследствие их износа. Выделим две основные причины, из-за которых происходит износ колес и рельсов: неправильное положение направляющих (рельсов) и движение крана с перекосом, в частности при неточной установке его ходовых колес.
Второй причине посвящена статья . Рассмотрим первую причину.
Допуски на отклонения направляющих путей кранов мостового типа, приведенные в действующих нормативных документах, имеют расхождения, содержат ряд неточностей и ошибок . Это затрудняет принятие правильного решения о необходимости рихтовки направляющих. Отсутствуют указания о том, что при оценке значимости отклонений направляющих следует учитывать их взаимодействие с ходовыми колесами крана (задевают или нет реборды колес за головки рельсов, наблюдается или нет буксование в начале движения грузовой тележки или крана).
Встречаются случаи, когда отклонения направляющих выходят за пределы допусков, но рихтовка не обязательна (иногда даже противопоказана), и наоборот: отклонения направляющих не превышают допуски, но рихтовка явно необходима.
Отметим, в частности, что нормы отклонений направляющих путей опорных мостовых кранов, приведенные в Правилах ПБ 10-382-00, не учитывают ряд факторов, от которых зависит нормальная работа крана, а именно:
Ширину колеи кранового пути;
Расстояние между колоннами;
Фактический пролет крана;
Не регламентированы отклонения от прямолинейности путей мостовых кранов.
Ниже использованы нормы отклонений направляющих, взятые из документов, утвержденных Ростехнадзором или согласованных с ним. Кроме того, использованы рекомендации из «Справочника по кранам» и нормы из ISO 12488-1:2005(Е) .
Условные обозначения:
L - пролет крана;
L ф - фактический пролет крана;
L б – длина подкрановой балки;
К - ширина колеи кранового пути (расстояние между осями направляющих);
К - уширение (сужение) колеи;
S - расстояние между осями колонн (шаг колонн);
H п.с. - разность отметок направляющих в одном поперечном сечении;
H с.к. - разность отметок направляющих на соседних колоннах;
i в – продольный уклон пути (тангенс угла наклона в вертикальной плоскости);
i п.с. – поперечный уклон пути (тангенс угла наклона) в одном поперечном сечении.
Обоснование рихтовки по критерию «Разность отметок рельсов в одном поперечном сечении (поперечный уклон пути)»
1.1. Пути мостовых кранов
В Правилах ПБ 10-382-00 для путей мостовых кранов приведена норма допускаемой разности отметок головок рельсов в одном поперечном сечении [?h п.с. ] = 40 мм. Данная норма не зависит от ширины колеи пути, следовательно, не отражает условия работы кранов, имеющих разный пролет.
В РД 50:48:0075.03.05 приведена норма 0,005 К, но не более 40 мм. Соотношение 0,005 К теряет смысл для кранов, имеющих пролет более 8 м.
В ISO 12488-1:2005(Е) для путей 3 класса допуска (стационарные крановые пути при пробеге кранов до 10 000 км) приведена норма: [?h п.с. ] = 2К, но не более 20 мм. Величина К берется в м.
В «Справочнике по кранам» приведена норма максимального уклона, рекомендуемого при проектировании механизмов передвижения грузовых тележек, = 0,002 (тангенс угла наклона направляющих тележечного пути). Данная норма предполагает сохранение сцепления ходовых колес грузовой тележки с направляющими тележечного пути.
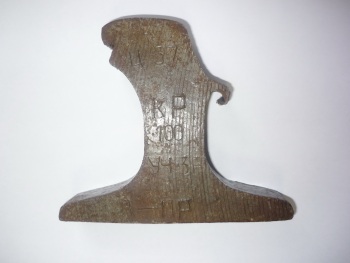
1.2. Пути козловых кранов
В Правилах ПБ 10-382-00 для путей козловых кранов пролетом до 30 м приведена норма разности отметок головок рельсов в одном поперечном сечении 40 мм, а при пролетах 30 м и более – 50 мм.
В РД-10-117-95 для путей козловых кранов норма дана в зависимости от класса точности пути, отражающего режим работы механизма передвижения крана, а именно: 20, 30, 40, 50 мм. Данная норма не зависит от ширины колеи.
В ГОСТ Р 5124-99 приведена норма поперечного уклона [ i п.с. ] = 0,01. Данная норма неприемлема. Кран может сдвинуться в сторону более низкого рельса.
В РД 50:48:0075.01.05 норма допускаемой разности отметок в одном поперечном сечении 0,005 К, но не более 40 мм. При таком ограничении соотношение 0,005 К теряет смысл для кранов, имеющих пролет более 8 м.
В ISO 12488-1:2005(Е) для путей 3 класса допуска [?h п.с. ] = 2К, но не более 20 мм. Величина К берется в м. Соотношение 2К теряет смысл для кранов, имеющих пролет более 10 м.
В «Справочнике по кранам» приведена норма максимального уклона, рекомендуемого при проектировании механизмов передвижения грузовых тележек, а именно 0,002. Данная норма предполагает сохранение сцепления ходовых колес грузовой тележки с направляющими, что актуально для грузовых тележек с моторным приводом механизма передвижения. Для грузовых тележек с канатным приводом механизма передвижения уклон не имеет значения для сцепления колес с направляющими. От величины уклона зависит только усилие в тяговом канате.
Выводы. При оценке необходимости рихтовки направляющих путей мостовых и козловых кранов по критерию «Разность отметок рельсов в одном поперечном сечении (поперечный уклон пути)», когда механизм передвижения грузовой тележки расположен на ней самой, целесообразно проверить три условия:
1) (?h п.с. / К ) ? 0,002; при этом надо учитывать возможный уклон вследствие строительного подъема (остаточного отрицательного прогиба) пролетных балок мостового крана или верхнего пролетного строения козлового крана;
2) сцепление колес грузовой тележки с направляющими тележечного пути не нарушается, то есть колеса грузовой тележки не буксуют в начале движения;
3) кран не сдвинулся в сторону более низкой направляющей, то есть износ реборд ходовых колес (наружных реборд на более высокой стороне крана и внутренних на более низкой стороне) и соответствующих боковых поверхностей направляющих не наблюдается.
Для путей козловых кранов, у которых грузовая тележка передвигается за счет канатной тяги, имеет смысл проверить только третье условие.
Обоснование рихтовки по критерию «Разность отметок направляющих на соседних колоннах (продольный уклон пути)»
2.1. Пути мостовых кранов
В Правилах ПБ 10-382-00 указана норма разности отметок рельсов на соседних колоннах?h с.к. = 10 мм. Чаще всего расстояние между осями колонн (шаг колонн S) равно 6 м. Если подкрановые балки не имеют прогиба в вертикальной плоскости, то при?h с.к. = 10 мм и S = 6 м продольный уклон пути равен 0,0017. Практика показала, что при данном уклоне кран движется нормально, без потери сцепления колес с рельсами. Следовательно, нет никакого смысла выравнивать положение направляющих по высоте, если уклон не превышает 0,0017. Этот показатель целесообразно распространить на все другие случаи, когда шаг колонн не равен 6 м. Например, при шаге колонн 24 м, прямых подкрановых балках и разности отметок на соседних колоннах, не превышающей 40 мм, рихтовка направляющих в вертикальной плоскости не обязательна.
В РД 50:48:0075.03.05 норма разности отметок направляющих в ряду вдоль пути указана 0,0015 L б. При этом разность отметок не должна превышать 10 мм, если L б? 10 м, и 20 мм, если L б > 10 м.
В ISO 12488-1:2005(Е) для путей 3 класса допуска норма отклонения от прямолинейности пути в вертикальной плоскости дается 4 мм на 2 м пути, что соответствует уклону i в = 0,002.
В «Справочнике по кранам» приведена норма максимального уклона, рекомендуемого при проектировании механизмов передвижения мостовых кранов, i в = 0,001. Данная норма предполагает сохранение сцепления ходовых колес крана с направляющими.
В практике обследования крановых путей мостовых кранов встречались следующие случаи:
· Разность отметок на соседних колоннах превышает норму. Шаг колонн больше 10 м. Подкрановые балки прямые. Кран передвигается без затруднений (без потери сцепления колес с рельсами). Необходимо определить продольный уклон пути. Пример: ?h с.к. = 35 мм; S = 24 м;
I в = 0,0014. Рихтовка не обязательна.
· Разность отметок направляющих на соседних колоннах не превышает норму, прогиб подкрановых балок не превышает норму, однако крановщик жалуется, что кран с трудом выезжает из «ямы». По СНиП 2.01.07-85 допускаемая величина прогиба подкрановых балок в вертикальной плоскости для групп режима работы крана 1К…6К равна 1/400 от длины балки. В частности, при S = 6 м, ?h с.к. = 10 мм и прогибе подкрановых балок в вертикальной плоскости 15 мм продольный уклон на участке такого пути между осью колонны и серединой пролета между колоннами равен 0,0067, то есть примерно в 4 раза больше значения, при котором сцепление колес с рельсами не нарушается. Рихтовка необходима.
2.2. Пути козловых кранов
В Правилах ПБ 10-382-00 указана допускаемая разность отметок рельсов 30 мм на 10 м длины пути. Практика показала, что, если данная норма выполняется, кран передвигается без затруднений.
В РД-10-117-95 даны допускаемые отклонения от прямой линии от 10 до 60 мм в зависимости от класса точности пути без указания длины участка пути, на котором данное отклонение измеряется. Это делает невозможной оценку продольного уклона. В этом же документе приведена норма на отклонение от прямой линии на участке пути длиной 2 м, а именно 2…5 мм в зависимости от класса точности пути, что соответствует уклону 0,001…0,0025.
В ГОСТ Р 51248-99 приведена норма продольного уклона пути 0,01. Данная норма неприемлема. При указанном уклоне кран передвигаться не сможет.
В РД 50:48:0075.01.05 приведена норма допускаемой разности отметок 0,003 В. При этом разность отметок не должна превышать 30 мм. В качестве величины В рекомендовано брать: базу крана или половину длины инвентарной секции рельса, или 5 м.
Нечеткое толкование величины В затрудняет определение нормы допуска по данному документу.
В ISO 12488-1:2005(Е) для путей 3 класса допуска норма отклонения от прямолинейности в вертикальной плоскости дается 4 мм на 2 м пути, что соответствует уклону 0,002.
В «Справочнике по кранам» приведена норма максимального уклона, рекомендуемого при проектировании механизмов передвижения козловых кранов, i в = 0,003. Данная норма предполагает сохранение сцепления ходовых колес крана с направляющими. Она совпадает с нормой в Правилах ПБ 10-382-00.
Выводы. При оценке необходимости рихтовки по критерию «Разность отметок направляющих на соседних колоннах (продольный уклон пути)» целесообразно проверить условия:
1) i в? = 0,0017 для путей мостовых кранов; определять уклон необходимо с учетом возможного прогиба подкрановых балок;
2) i в? = 0,003 для путей козловых кранов;
3) сцепление колес крана с направляющими не нарушается, то есть колеса не буксуют в начале движения.
Если данные условия выполняются, рихтовка не обязательна.
Обоснование рихтовки по критерию «Сужение (расширение) колеи»
В Правилах ПБ 10-382-00, РД-10-117-95, ГОСТ Р 51248-99, РД 50:48:0075.03.05, РД 50:48:0075.01.05 приведена норма сужения (расширения) колеи: ?к = 15 мм. Для путей козловых кранов, имеющих пролет 30 м и более, в ПБ 10-382-00 и РД 50:48:0075.01.05 приведена норма?к = 20 мм.
В ISO 12488-1:2005(Е) для путей 3 класса допуска норма сужения (расширения) колеи равна ± 8 мм для пролетов кранов L ? 16 м и ± мм для других пролетов, но не более 20 мм.
В практике обследования крановых путей встречались следующие особые случаи:
· Сужение (расширение) колеи значительно превышает норму, но кран ездит нормально, износа боковых поверхностей направляющих и реборд ходовых колес не наблюдается. Данный случай встречается, когда фактический пролет мостового (или козлового) крана отличается от паспортного значения (L ф? L), а рельсы уложены правильно (не по паспортному значению ширины колеи кранового пути, а по фактическому пролету крана). Рихтовка в плане противопоказана.
· Сужение (расширение) колеи меньше нормы, но кран заклинивает, наблюдается интенсивный износ направляющих и ходовых колес. Это случай, противоположный рассмотренному выше, то есть путь уложен по паспортному значению ширины колеи, а требовалось уложить его по фактическому пролету крана. Рихтовка в плане необходима.
· Сужение (расширение) колеи превышает норму, кран заклинивает, наблюдается интенсивный износ направляющих и ходовых колес крана. В данной ситуации вначале следует выяснить, что является причиной заклинивания: рельсовый путь или кран. Среди причин, относящихся к крану, наиболее вероятной является неправильная установка ходовых колес. До принятия решения о рихтовке направляющих в плане необходимо произвести измерение положения ходовых колес крана и их выверку. В 90 % случаев после выверки ходовых колес кран начинает ездить нормально. Если после выверки ходовых колес их реборды не задевают за головки рельсов, то рихтовка в плане не требуется.
Из сказанного следует, что выводы о состоянии кранового рельсового пути можно делать лишь при комплексном подходе к изучению ситуации, то есть обследовать не только рельсовый путь, но и его взаимодействие с ходовыми колесами крана.
Обоснование рихтовки по критерию «Отклонение от прямолинейности направляющих в плане (угол отклонения)»
В Правилах ПБ 10-382-00 норма отклонения от прямолинейности направляющих в плане отсутствует. Можно было бы предположить, что данный дефект направляющих не влияет на работоспособность крана. Это глубоко ошибочно. Исследования немецких ученых показали, что при тангенсе угла отклонения направляющей 0,002 и более поперечное усилие, действующее на колесо, составляет приблизительно одну пятую часть от величины вертикального давления колеса на рельс. В этом случае интенсивный износ реборд колес и рельсов неизбежен .
В старых Правилах норма отклонения от прямолинейности была 20 мм на участке пути длиной 40 м для путей мостовых кранов и на участке 30 м для путей козловых кранов. Тангенсы соответствующих углов отклонения равны 0,0005 и 0,0007.
В ГОСТ Р 51248-99 для козловых кранов с жесткими ходовыми рамами норма отклонения от прямолинейности дается 20 мм на длине 10 м, что соответствует тангенсу угла отклонения 0,002.
В РД-10-117-95 норма отклонения от прямолинейности направляющих на длине 2 м равна 2, 3, 4, 5 мм в зависимости от класса точности пути. Соответствующие значения тангенса угла отклонения равны 0,001, 0,0015, 0,002, 0,0025.
В РД 50:48:0075.03.05 приведена норма отклонения направляющей от прямой линии 30 мм, но не сказано, на какой длине надо определять это отклонение.
В этом же документе приведена норма допускаемой кривизны направляющей 3 мм на длине 2000 мм, что соответствует тангенсу угла отклонения 0,0015.
В РД 50:48:0075.01.05 данная норма отсутствует.
В ISO 12488-1:2005(Е) для путей 3 класса допуска норма отклонения от прямолинейности направляющих на длине 2 м дается 2 мм, что соответствует тангенсу угла отклонения 0,001.
Выводы:
1. В нормативных документах Ростехнадзора целесообразно восстановить норму отклонения от прямолинейности направляющих путей мостовых и козловых кранов.
2. В качестве нормы отклонения от прямолинейности направляющих целесообразно принимать:
Для путей мостовых кранов – тангенс угла отклонения 0, 001;
Для путей козловых кранов - тангенс угла отклонения 0,002.
При превышении данных значений требуется рихтовка направляющих в плане.
Приведенные рекомендации по обоснованию необходимости рихтовки рельсовых путей мостовых и козловых кранов апробированы на ряде предприятий Свердловской области. Их использование позволило предприятиям в ряде случаев сэкономить значительные средства.
Литература:
- 1.Птухин С.В., Кузнецов Е.С. Контроль положения и установка ходовых. Кузнецов Е.С. Крановым путям – должное внимание// Эксперт РСП, 2009, № 2, с. 38.
- 2.ПБ 10-382-00 Правила устройства и безопасной эксплуатации грузоподъемных кранов.
- 3.ГОСТ Р 51248-99 Пути наземные рельсовые крановые. Общие технические требования.
- 4.РД-10-117-95 Требования к устройству и безопасной эксплуатации рельсовых путей козловых кранов.
- 5.РД 50:48:0075.03.05 Рекомендации по устройству и безопасной эксплуатации надземных крановых путей. – М.: ЗАО НПЦ «Путь К».
- 6.РД 50:48:0075.01.05 Рекомендации по устройству и безопасной эксплуатации наземных крановых путей. – М.: ЗАО НПЦ «Путь К».
- 7.Справочник по кранам: В 2 т. Т. 2. Характеристики и конструктивные схемы кранов. Крановые механизмы, их детали и узлы. Техническая эксплуатация кранов/ М.П. Александров, М.М. Гохберг, А.А. Ковин и др.; Под общ. ред. М.М. Гохберга. – Л.: Машиностроение. Ленингр.отд-ние, 1988.
- 8.ISO 12488-1:2005(Е) Краны – Допуски для колес и для продольных и поперечных крановых путей – Часть 1: Общие положения.
- 9.СНиП 2.01.07-85 Нагрузки и воздействия.
- 10.Г. Пайер, М. Шеффлер, Х. Кильхорн и др. Грузоподъемные краны: В 2-х кН. Кн. 1/ Сокр. пер. с нем. М.М. Рунова, В.Н. Федосеева; Под ред. М.П.Александрова. – М.: Машиностроение, 1981.
- 11.Птухин С.В. Новая методика контроля положения ходовых колес грузоподъемных кранов// Эксперт РСП, 2010, № 6, с. 42.
4.1. Содержание раздела распространяется на:
подвесные ручные и электрические краны (в том числе краны-штабелеры);
мостовые ручные и электрические краны общего назначения, специальные (магнитные, грейферные, с гибким подвесом траверсы, поворотной тележкой, подхватом), металлургические (заливочные, литейные, для раздевания слитков, колодцевые, ковочные и т.д.);
оборудование грузовых монорельсовых дорог промышленного транспорта.
4.2. Мостовые краны монтируют после сдачи по акту подкрановых путей в полном объеме или отдельными участками.
Допускается приемка отдельного выверенного участка подкрановых путей длиной не менее трех баз крана с установкой по концам этого участка временных тупиковых упоров. Допускаемые отклонения от проектных размеров смонтированных подвесных путей приведены в табл. 2, подкрановых - в табл. 3.
Таблица 2
Отклонения для подвесных путей | |
Отклонения стенки двутавровой балки от вертикальной плоскости при высоте балки h | 0,01h |
Горизонтальное смещение оси нижней полки относительно разбивочной оси пути | 3 |
Разность отметок нижнего (ездового) пояса на соседних опорах (вдоль пути) при расстоянии между опорами L |
1/1500 L |
Разность отметок нижних (ездовых) поясов соседних балок (в пролетах) в одном поперечном сечении: |
|
На опорах В пролете | |
для путей двух- и многоопорных кранов | 6 10 |
то же, со стыковыми замками | 2 2 |
Взаимное смещение торцов нижних полок в стыках по высоте и в плане | 1 1 |
Таблица 3
Отклонения для подкрановых путей мостовых кранов | Размеры допускаемых отклонений, мм |
Смещение оси рельса относительно оси подкрановой балки, мм | 15 |
Расстояние между осями подкрановых рельсов (колея крана), мм | 10 |
Непрямолинейность оси рельса, мм, на длине 40 м | 15 |
Разность отметок головок рельсов на соседних колоннах, мм, при расстоянии между колоннами L: |
|
L < 10 м | 10 |
L > 10 м | 0,001 L, но не более 15 |
Разность отметок головок рельсов в одном поперечном сечении пути: | |
на опорах | 15 |
в пролете | 20 |
Взаимное смещение торцов рельсов в стыках по высоте и в плане | 2 |
4.3. Метод и порядок монтажа мостовых кранов определяется ППР или технологической запиской в зависимости от массы крана и отдельных его узлов, габаритных размеров крана и цеха, а также наличием монтажных механизмов на строительной площадке.
Мостовые краны общего назначения можно монтировать в сборе или отдельными узлами (два полумоста, тележка и кабина).
Порядок монтажа большинства металлургических и специальных кранов зависит от конструктивного их исполнения и условий поставки.
Рекомендуемая последовательность сборки этих кранов:
подъем моста отдельными узлами;
подъем и установка тележки (одной или двух) в сборе или отдельными частями;
сборка и выверка моста и тележки;
подъем кабины и других узлов крана;
запасовка канатов и подвешивание подъемного полиспаста крана;
испытание и сдача крана.
4.4. При поступлении в монтаж кранов отдельными элементами на площадке до подъема элементы крана укрупняют в блоки в соответствии с грузоподъемностью монтажного механизма. При этом учитывают массу электрооборудования, так как электрооборудование поднимают одновременно с узлом крана.
4.5. После стыковки моста на монтажных болтах замеряют его геометрические размеры; при соответствии фактических размеров проектным стыки соединяют согласно проекту на болтах, сварке или заклепках.
4.6. Собранное болтовое соединение проверяют щупом; пластина щупа толщиной 0,3 мм должна входить под накладку на глубину не более 20 мм.
4.7. При сборке конструкций под сварку должна быть обеспечена точность соединений в пределах допусков, предусмотренных проектом. Сварку металлических конструкций кранов и контроль качества сварки производят согласно правилам Госгортехнадзора СССР и техническим условиям завода-изготовителя.
4.8. Требования, предъявляемые к установке заклепок, приведены в табл. 4.
Таблица 4
Наименование дефекта | Допускаемые значения |
Вибрация или перемещение головки под ударами контрольного молотка | Не допускается |
Неплотное прилегание головки к склепываемому пакету | Щуп толщиной 0,2 мм не должен проходить вглубь под головку более чем на 3 мм
|
Трещиноватость или рябина головки | Не допускается |
Зарубки на головке | Не более 2 мм |
Смещение головки с оси стержня | |
Маломерная и недооформленная по высоте головка | Не более 0,05 диаметра головки и не более 0,1 диаметра стержня на всю головку |
Венчик вокруг головки | Толщиной не менее 1,5 мм и не более 3 мм. Венчик толщиной менее 1,5 мм следует срубить |
Зарубка поверхности металла обжимкой | Не допускается |
Неполное заполнение головкой потайной заклепки по диаметру головки | Не более 0,1 диаметра стержня |
Избыток или недостаток по высоте потайной заклепки | Не более 0,5 мм, при необходимости избыток зачистить |
4.9. Поставленные заклепки с отклонениями выше значений, приведенных в табл. 4, бракуют и заменяют.
4.10. Установленная на мост крана грузовая тележка должна опираться на все колеса. Разность расстояний между осями колес (база тележки), измеренная по двум сторонам, не должна превышать 2 мм.
4.11. Если поверхности катания подтележечных рельсов расположены не на одном уровне, обеспечивающем опирание всех ходовых колес тележки, разрешается под рельсы над диафрагмами балок установить подкладки толщиной до 20 мм.
4.12. Систему централизованной смазки монтируют в соответствии с инструкцией завода-изготовителя.
4.13. Кабину монтируют после установки в ней электрооборудования и системы управления.
4.14. По окончании монтажа крана проверяют его фактические размеры. Отклонение практических размеров должно соответствовать допускам, предусмотренным заводской документацией, а при отсутствии их не превышать значений, приведенных в табл. 5.
Таблица 5
Контролируемый размер | Допуски, мм |
Пролет крана: | |
при длине пролета до 34 м | 5 |
при длине пролета, 34 - 50 м | 6 |
при длине свыше 50 м | 7.5 |
Разность диагоналей моста | 5 |
Колея тележки: | |
при ширине до 7500 мм | 3 |
при ширине свыше 7500 мм | 5 |
Разность диагоналей тележки | 3 |
Разность отметок головок подтележечных рельсов в поперечном сечении при колее тележки, мм |
|
до 3100, а также независимо от колеи тележки у колодцевых кранов, для раздевания слитков, мульдозавалочных |
5 |
от 3100 до 7500 | 8 |
свыше 7500 | 10 |
Смещение торцов подтележечных рельсов в стыках по высоте и в плане | 1 |
Отклонение от горизонтальной плоскости крайних точек наружной плоскости катков | 1 мм на 1 м |
4.15. При монтаже специальных кранов (колодцевых и для раздевания слитков), имеющих шахту, последнюю присоединяют к раме тележки после ее установки на мосту крана. Распорки (пауки) внутри шахты срезают только после соединения шахты с тележкой.
Перед подъемом шахты в вертикальное положение во избежание поворота шахты на 180° следят за монтажными рисками, указанными на сборочном чертеже, корпусе шахты и раме тележки, которые должны быть одинаково ориентированы.
Кронштейны для кабин и площадок на шахте, а также сами кабины, как правило, следует устанавливать до подъема шахты.
4.16. Отклонение рабочих плоскостей шахты от линии отвеса не должно превышать 3 мм на всю длину шахты. После закрепления шахты к раме тележки монтируют оборудование внутри шахты согласно заводской инструкции.
4.17. Монтаж специальных кранов с лапами на траверсе осуществляют аналогичным способом. После монтажа моста и тележки под ними собирают шахту и траверсу, поднимая их с помощью полиспастов.
4.18. Механизмы верхней тележки собирают согласно чертежам, обращая внимание на оси конических катков механизма поворота, которые должны лежать в горизонтальной плоскости, параллельной плоскости кругового рельса.
Боковые ролики устанавливают с зазором 1-1,5 мм к внутренней поверхности кругового рельса. Наименьший зазор между нижней точкой бокового ролика и рамой тележки 10 мм. Положение траверсы регулируют так, чтобы ее продольная ось при подъеме и опускании была горизонтальной; отклонение не должно превышать 1 мм на 1 м длины траверсы.
4.19. При запасовке канатов механизмов подъема необходимо соблюдать "Правила устройства и безопасной эксплуатации грузоподъемных кранов" Госгортехнадзора СССР.
Монтаж оборудования грузовых монорельсовых дорог промышленного транспорта
4.20. Оборудование грузовых монорельсовых дорог (тали стационарные, передвижные с ручным приводом или с электроприводом, с управлением снизу или из кабины) заводы-изготовители поставляют, как правило, в сборе. Отдельным узлом поставляют кабину управления.
4.21. К монтажу талей приступают после приемки пути (монорельса). Требования, предъявляемые к однорельсовому пути:
балки пути к фермам или конструкциям перекрытия крепят болтами в соответствии с проектом;
смещение торцевых профилей на стыках не должно превышать 2 мм, а зазор между торцами балок - 3 мм;
4.22. После установки тали зазор между ребрами полки монорельса и ребордами колес тали должен составлять 2-3 мм.
4.23. У талей с управлением из кабины после подъема тали устанавливают кабину и соединяют с тележкой тали.
4.24. По окончании монтажа таль испытывают в соответствии с требованиями заводской документации и правил Госгортехнадзора.
4.25. Оборудование межцехового транспорта (электротягачи и др.) монтируют в соответствии с указаниями по монтажу электроталей (см. пп. 4.20 - 4.24 настоящей инструкции).
На 25% сокращает срок его службы вдвое. Повышение нагрузки на 50% сокращает продолжительность работы, подшипника в десять раз, отсюда стремление перейти к сварным стыкам подкрановых рельс. Такой переход впервые был осуществлен на Верхне-Исетском заводе в 1957 г. Обследование мостовых кранов на Магнитогорском металлургическом заводе, работающих на подкрановых рельсах со сварными стыками, показало, что износ крановых колес сократился на 30%.
Независимо от конструкции рельсы подкрановых путей, как это требуют Строительные нормы и правила (СНиП III-B. 5-62) должны быть смонтированы так, чтобы отклонения их положения от проектных размеров не выходили за пределы приведенных в табл. 4 допусков.
Размеры подкрановых рельсов и рекомендации их для кранов определенной грузоподъемности выбраны исходя из размеров крановых колес. Например, для крана со средним (С) режимом работы, колесами диаметром по поверхности катания 700 мм рекомендуется крановый рельс типа КР-1100. Ширина поверхности катания у такого колеса составляет 130 мм, а зазор между ребордами колеса и рельсов на одну сторону составляет (130 -100) :2= 15 мм. Пролет между подкрановыми рельсами измеряют стальной рулеткой с точностью до 4 мм (рулетка длиной 20 м); мост крана по длине пролета изготовлен с допуском 5 мм. Таким образом, при неблагоприятном сочетании знаков допусков (одинаковые знаки) отклонение от проектного размера может составить 10+5+4=19 мм. Это больше чем предусмотрено конструкций колес на 19-№=4 мм.
Приведенное сочетание отклонений от проектных размеров можно рассматривать как критический случай. Практически такого сочетания почти не может быть: знаки отклонений будут обязательно разные. Это сочетание отклонений взято, чтобы показать, как важно не только не выходить из пределов допусков, но и стремиться смонтировать подкрановые рельсы не с предельным значением допусков, а с наименьшими возможными. Измерять пролет подкрановых рельсов надо тщательно, чтобы погрешность измерения была минимальной. Лучших результатов достигают в том случае, когда монтаж подкрановых рельсов поручают монтажникам, которые монтируют мостовой кран: они хорошо понимают значение точности укладки рельсов и выполняют такую укладку более тщательно.
Независимо от исполнителей подкрановые пути должны быть сданы для монтажа мостового крана. Сдачу оформляют соответствующим актом, к которому прикладывают монтажный формуляр подкрановых путей (исполнительную схему) с проектными и фактическими размерами в плане и по высоте, как это Требуется согласно приведенным в табл. 4 данным.
Допуски на монтаж подкрановых путей
Вид отклонений | Допуск в мм |
---|---|
Расстояния между осями подкрановых рельсов одного пролета Смещения оси рельсов с оси подкрановой балки Отклонения оси рельса от прямой по длине участка 40 м Разности отметок головок рельсов в одном пролете: на опорах в пролете Разность отметок рельсов на соседних колоннах: при расстоянии между колоннами, 1 м при l менее 10 м |
10 15 15 |